We fabricate Swagelok components for our customers. This can range from providing simple tube bends to building turnkey panels designed to control complex gas mixtures and flows that are then installed by the customer.
Where are the pictures?
Much of what we are fabricating belongs to the customer and whilst we have often worked closely with them ensuring their designs meet their requirements - accuracy, flow, safety etc... we are unable to showcase the extent of the work we are producing. Often the designs are owned by the customer and protected by non-disclosure agreements (NDA's) therefore we cannot show these configurations in the public domain.
How clean is our facility?
All of the ultra high purity (UHP) assemblies we fabricate for the semiconductor industry are assembled in our ISO Class 6 Cleanroom. We work to industry standards of workmanship and testing as well as to customers specific requirements such as Helium Leak testing (shown below), nitrogen purged double-bagged packaging etc; including specific Certification and Standards - products assembled in our clean room are shipped in line with end-user requirements ready for final assembly.
Repeat-ability and repeat orders
We can assemble standard, cost effective configurations and sub-assemblies with precision. The production set-up we have for these repeat orders ensure a cost-saving for our customers - our experienced fabricators have thousands of man hours bending tube, welding, and assembling components. Consistently delivering batches of correctly assembled parts maximises yield, reduces wastage and error during final assembly of our customer’s equipment.
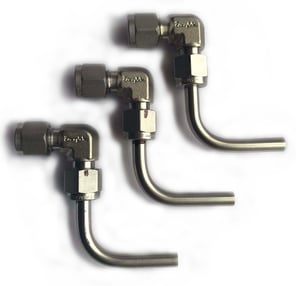
Orbital welding
Where a compact, lightweight assembly with the highest leak integrity is required, Orbital welding the assembly may provide the answer. In the assembly below the welding allowed for a continuous tube run – where we would have historically used tube connectors. The ability to orbitally weld the tubing allows for an optimised footprint assembly that is both strong and lightweight and the Bill Of Materials is also reduced.
Cost-benefit
We assess and measure the cost-benefit of our assemblies both before and after manufacture. Often the configurations arise from discussions with our Field Engineers via our business development managers in conjunction with ongoing dialogue with customer representatives – everyone who contacts us at Swagelok Bristol is put in touch with their area manager who will support your issues.
Start the Conversation
Early engagement and discussions with our team around the designs and design optimisation has been shown to provide a cost saving for our customers through improved manufacturability, alternative component suggestions and routing efficiency reviews.
We discuss the successes we have within each industry with our customers and share our knowledge on best-practice and conformance. We have ideas and real alternatives that can ensure safety and economic benefits to our customers.